staff member:
As the “organism†that is the most direct contact with drugs, the staff entering the production workshop must not have wounds on their bodies, except for the basic requirements (no mental illness, infectious diseases, etc.), and must not leave long hair and long nails. No makeup, or even jewelry, watches, pens, etc. Usually, before entering the production workshop, the staff need to put on cleaned clothes, masks and white running shoes, and wash hands with 75% alcohol.
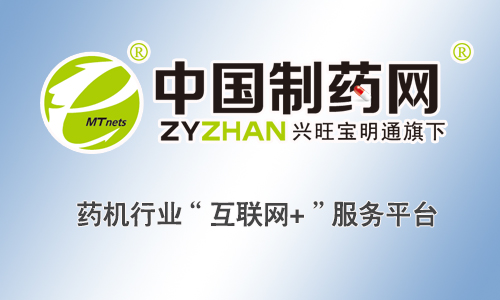
Buffer room:
In the highly clean production workshop, in order to maintain the absolute hygiene of the clean room of the drug production, the operator will also use the air pressure to create a buffer room to protect the clean environment of the clean room.
This buffer room is located between the clean room and the corridor. There are often single and double doors. Single doors are used for walking people. Double doors are used for transporting materials and people are separated. The air pressure in this buffer room is slightly higher than the clean rooms and corridors on both sides, and the doors leading to the clean room and the corridor cannot be opened at the same time. In this way, in the case of unbalanced air pressure, the air in the corridor and the air in the clean room will not enter the buffer room with higher air pressure because of the lower air pressure, so that the low design on both sides of the middle side avoids cross-contamination of the air between the two sides.
air:
Creating a clean factory that meets standards is not only a big investment, but also the operating costs are not to be underestimated. Generally speaking, in the pharmaceutical production workshop, in addition to disinfection and sterilization, even the air needs to meet the three-level purification standards. For this reason, the staff often joked that the last thing they worry about is the haze day to the body. The impact, because they may breathe the highest level of pure air on the planet.
In addition, pharmaceutical plants need to be equipped with wastewater treatment equipment and pipelines, fire protection systems, power distribution systems, automatic control systems, vacuum cleaning systems, etc., and the investment in these equipment is tens of millions, and hundreds of millions The equipment for air heat and humidity treatment and air distribution is more expensive, consumes more electricity, and is expensive to operate.
In order to maintain a long-lasting clean environment, all of the pharmaceutical factory's clean area air conditioners need to operate 24 hours to maintain the pressure difference in the clean area to avoid damage to cleanliness. However, if many factories do not produce at night, they will generally set the air conditioner to the 'night duty' mode, and reduce the number of air changes to ensure cleanliness, thus achieving the goal of energy saving and GMP compliance.
What is the problem with air conditioning shutdown? It is generally believed that after the clean air conditioner is shut down, the cleanliness of the workshop will be quickly destroyed. After a period of time (such as 8 hours), it will be used again. It takes a long time to recover from self-cleaning. After the self-cleaning sampling test of the number of particles and microorganisms is carried out, it is considered that the cleanliness is qualified and can be normally produced.
However, factories that generally require frequent production will not do this. Unless the factory has not been produced for a long time, such as ten days and a half, it may consider downtime, such as the annual overhaul of the factory.
Water and land:
The location of pharmaceutical factories often requires not only geographical location, taxation, and industry policies. They even need to refer to historically left-end pollution to assess environmental risks, such as water quality testing (in fact, this action is also required after the plant is completed). Every year), in order to understand the soil and underground pollution, do not underestimate this link, the cost of all the factories of large pharmaceutical companies can add up to 300 million to 400 million yuan per year.
we can supply many types auxiliary and main engine spare parts ,
especially for the liner ,cover ,piston ,and
it is full range of piston for the following type :
AAA) YANMAR DIESEL ENGINE
K(D)L, KFL-T, 6MAL-H/T/HT/DT, S165-T/ST/EN,
S185-ST/UT/ET, M200L-UN/SN/EN/M220L-UN/SN/EN / N 330
BBB) DAIHATSU DIESEL ENGINE
PS22/26/ DS18(A)/ DS(B)22/
DL20/22/28/ DK20 / DK 28
CCC) NIIGATA DIESEL ENGINE
6L(M)25BX/6M28AFTE/BX/6M31X/EZ/EX/ 31AFTE /34AGT
DDD) AKASAKA
AH30/AH38/ AH40/D/F/ A31/34/37/41/ DM28/30/33/36/38/40(A)K/ DM46/ UEC37H-HB/ UEC 37/88H
UEC 37LA/ UEC45LA/ UEC52LA/ UEC52HA/ UEC60HA/ UEC60LS/ UEC45HA/115 ALL UET TYPE
EEE) MITSUBISHI (KOBE AND AKASAKA )
45/75C/ 45/80D/ 52/90D/ 52/105D.E/
UEC37H-IIB/ UET37/88HA/UEC45HA.LA/ UEC52HA.LA/ S6B/
ETC
FFF) HANSHIN
6LU(D)26/ 6LU(N)28A/ 6LU(D)32/6LU(D)35/ 6LU(S)38/ 40 / 6LU40/ 6LU46A/ 6LU50A/
6EL30/ EL(S)32 /6EL(S)35/ 6EL38/ 6EL40/ 6EL(S)44/50A/
GGG) MAN B&W
S35MC/L35MCE/L50MCE/ L60MCE/ 40/54A
HHH) MITSUBISHI PURIFIER
SJ700~SJ1800/SJ 2000
III)SULZER
RND 68 RND 76 RD 44
JJJ) MAKITA
GSLH – 633 637 KSLH -633 637
Kkk) PIELSTICK
PC 2-5 PC 2-6
Engine Piston,Diesel Engine Piston,Engine Piston Parts,Engine Piston Spare Parts
ZhouShan HeCheng Machinery Co., LTD. , https://www.hcmarineparts.com